Service test cuts:
Halve pruning times with the right advice
Service test cuts: Halve cutting times with the right advice
Industry specialist MEBA offers its customers a very special service: an individual band saw blade check with the aim of increasing quality, productivity and effectiveness.
The results make you sit up and take notice. The service provided by the manufacturer of metal band sawing machines is such that customers send in their material and the MEBA band saw blade expert determines in a very complex process which band saw blade is the right one for this material and area of application. In a specific case*, a contract sawing company with an MEBApro 260 AP straight-cutting machine built in 2008 submits a rust- and acid-resistant material.
The issue: With a target of 420 cuts, the cutting performance of the machine is low (after 20 cuts) and the service life of the saw blade is short.
The customer would like recommendations on how to achieve greater efficiency.
*Exact data of the example
Material: 1.4301, diameter 80 mmSaw blade: MEBA Bi-Metal-SSaw blade price: 33,33 EUR/ pieceCutting parameters: Cutting speed 25 m/min, saw frame feed 12 mm/minCutting time: approx. 7 minutes
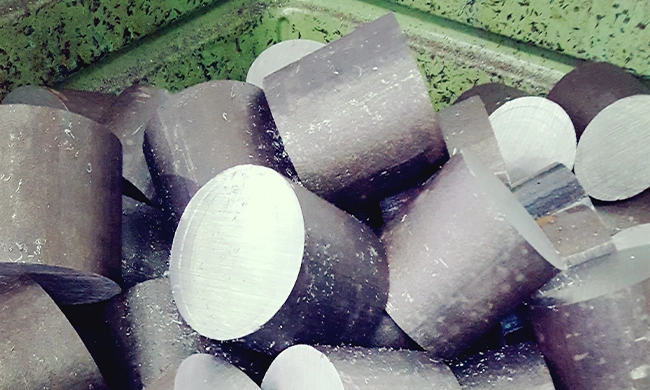
Amazing results thanks to the use of the right band saw blade
The MEBA band saw blade expert familiarizes himself intensively with the problem and carries out extensive tests with the customer’s material.
After the tests, it is clear to the expert that the MEBA H2 band saw blade is the right one for this specific example.
The band saw blade has an extra positive clamping angle and a powder-metallurgical, wear-resistant cutting material.
The price of the band saw blade is significantly higher than the one used previously.
However, these additional costs are worthwhile as the band saw blade increases efficiency many times over. Result: By using the recommended band saw blade, the cutting time can be reduced from 7 minutes to around 3.2 minutes and thus more than halved.
The material has a high-quality surface, which is also important for the subsequent machining process.
The test with MEBA H2 band saw blade in detail
- Cutting parameters (guide values): Cutting speed 35 m/min, saw frame feed 30 mm/min
- Coolant content (guide values): 10-15%
- Coolant content, measured on the machine: 15%
- Saw blade tension, measured with the MEBA saw blade tension measuring device: 220 N/mm²
- Saw in the saw band accordingly:
- 2 cuts with cutting speed 35 m/min, saw frame feed 10 mm/min
- 2 cuts with cutting speed 35 m/min, saw frame feed 15 mm/min
- 1 cut with cutting speed 35 m/min, saw frame feed 20 mm/min
- 2 cuts with cutting speed 35 m/min, saw frame feed 25 mm/min
- 1 cut with cutting speed 35 m/min, saw frame feed 30 mm/min
- Increasing the saw frame feed rate to 30 mm/min results in a slight cutting progression of approx. 0.2 mm. A reduction of the feed rate to 25 mm/min was achieved.
Result: A beautiful surface, cutting time: approx. 3.2 minutes
Other parameters are also important for the sawing result
In addition to the cutting time, the inspection also reveals other anomalies.
The specific example shows that a chip was drawn into the cutting channel during sawing.
For this reason, the adjustment of the chip brush was also recommended.
After sawing in the band saw blade and adjusting the cutting parameters, the series cut was successfully completed. Customer is very satisfied The extensive tests with corresponding recommendations and adjustments led to very positive customer feedback: “We have now sawn the entire quantity of 406 pieces of type 1.4301 steel with the recommended H2 band over 2.5 days,” says the customer.
“The belt could have done even more, but the material was sawn open. We deviated from the expert’s recommendations once, as the mixing ratio of 7 – 8 % was not correct due to negligence when filling the emulsion on the saw. Suddenly, noises could be heard and the cut became unclean. When we corrected this and brought the emulsion back to 14%, we were able to continue sawing with the band. The cutting quality improved immediately.”
Conclusion
Anyone using a metal band sawing machine should definitely pay attention to the saw blade quality and match the saw blade to the material.
With the right combination of sawing machine and band saw blade, it is actually possible to increase the efficiency of sawing many times over.
The “right” combination, i.e. the individually correct saw blade tension, the correct coolant content and the correct setting of the chip brush.
MEBA customers benefit from the valuable analysis of the saw blade expert.
They can submit materials and obtain a detailed, fact-based recommendation.
In this specific example, the cutting performance of the machine was doubled.
The service life has increased at least 20-fold.
The user receives high-quality blanks that are much easier to process than before, whether turning or milling.
And here again: sawing is the beginning of a successful end product… as the first step in the production chain, it lays the foundation for all further manufacturing processes.
Leave A Comment