The myth of the all-purpose belt:
Why the right band saw blade significantly increases your efficiency when sawing steel
The myth of the all-purpose band saw blade: Why the right band saw blade significantly increases your efficiency when sawing steel
Wherever steel and stainless steel is sawn, there is a widespread belief that a so-called universal band saw blade or universal saw blade can cover all cutting requirements for different materials such as flat steel, rectangular steel, pipes or angle iron. This assumption is based on the desire for a convenient solution. The aim is to minimize the effort involved in changing the saw blade and avoid having to purchase different types of saw blades for different sawing tasks. And yes, the supposed all-purpose solution sounds simple, but in other words it should save time and reduce costs.
But does the universal band saw blade really exist?
Let’s take steel construction for example. The day-to-day work of a steel fabricator requires a great deal of flexibility: small batch quantities, changing cross-sections, different shapes and dimensions of the workpieces and different types of steel are standard. Steel fabricators are under great time and cost pressure. And an efficient process is particularly important for one of the first steps in the production process, sawing. The desire for an all-purpose band saw blade is therefore very understandable.
But despite all the wishes, the reality is different: It disproves the myth of the universal band saw blade and shows that the use of suitable band saw blades for the respective sawing task is significantly more efficient and cost-effective, especially with changing workpiece dimensions and shapes.
We at MEBA have carried out extensive tests to back up this statement with facts. The tests show that the universal band saw blade cannot keep up in terms of cutting quality, speed and, above all, cost. This proves that it is worth choosing the right band saw blade, whether for large or small quantities. Find out more in this blog post.
The tests and their initial situation
As a manufacturer of metal band sawing machines, MEBA also has a high level of expertise in the field of band saw blades for metal processing. A highly specialized band saw blade expert has been established in the company, who carries out detailed consultations and individual test runs to find out which band saw blade is the right one for which sawing task.
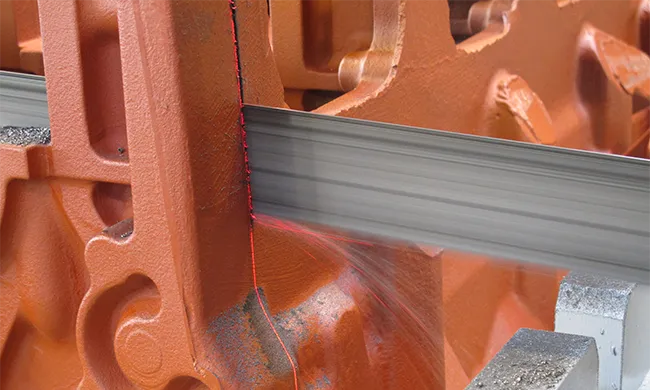
One of the most frequently asked questions to the expert is about the universal band saw blade, i.e. the one saw blade for steel that can do everything. During a customer visit, cutting tests were carried out in the sawmill with different saw blades and toothings and once again the customer did not believe that there is no “all-purpose blade” that can be used for all these sawing tasks.
During the test cuts, the customer saw live that a band saw blade was already broken after 15 cuts, while the expected service life with proper use was a few thousand cuts. Accordingly, the MEBA saw blade expert selected saw blades that were individually adapted to the sawing tasks and carried out further test runs with these blades. The tests were carried out on the MEBAeco 335 metal band saw. The machines in this series are as individual as the customer’s specific requirements. They are equipped with the patented double mitre system as well as clever technical features and can be networked and fully automated if required.
A total of 120 cuts were made per day with different profiles and material cross-sections. The variety of workpieces illustrates the challenges faced by the saw bands.
The tests and their analysis
Efficiency through specialized band saw blades: Strategy 1 versus Strategy 2
In the test runs, the effects on efficiency and costs of using a universal band saw blade (see table in download for strategy 1) compared to the targeted change of specialized band saw blades (see table in download for strategy 2) were investigated.
The sawing tests were based on the following parameters:
- Machine type: MEBA 335eco
- Saw blade dimensions: 4400x34x1.1 mm
- Type of band saw blade: Bi-metal
- Machine costs per hour: 50 euros
- Number of cuts per day:
Flat steel 200×20 mm: 20 cuts
Rectangle 60×60 mm: 20 cuts
Tube 100×6 mm: 20 cuts
Angle iron 80x80x6 mm: 20 cuts
U-steel 200 mm: 20 cuts
I-steel 200 mm: 20 cuts
Strategy 1: Use of a universal saw blade
The first strategy used a universal band saw blade with a 4/6 toothing and claw tooth geometry. The band saw blade remained in use for all workpiece types, regardless of the particular workpiece dimension or shape. Customers often work this way to save the time of changing the saw blade. However, the test series shows that this approach has some significant disadvantages. The total cost per shift amounted to 109.61 euros with a total time of 120.35 minutes per test run.
Strategy 2: Changing saw bands depending on workpiece dimensions
The second strategy is the specialized one: The saw blade is changed depending on the workpiece dimensions. The most suitable band saw blade is used for the respective workpiece. For example, a band saw blade with 2/3 serration was used for flat steel and one with 5/7 serration for pipes. The result: the total costs per shift fell to 87.12 euros, with a reduction in machine time to 98.69 minutes.
The results are astounding
The optimal choice of saw blade leads to optimized cutting performance, lower saw blade loads and a longer service life. The figures speak for themselves: the use of specialized saw bands reduces machine time by 18 % and tool costs by more than 50 %. Over 220 shifts, this results in a total saving of 4,875.40 euros and proves that cost optimization through the selection of the right band saw blade is significant.

Solid material (diameter 250 mm)
Because the tests already described were not enough, 5 cuts of solid material with a diameter of 250 mm were simulated in addition to the usual workpieces. This showed particularly clearly how the use of specialized band saw blades affects efficiency:
- Strategy 1: 671 machine hours, total costs of 36,951.80 euros
- Strategy 2: 495 machine hours, total costs of 26,151.00 euros
Strategy 2, i.e. changing the saw blade types depending on the workpiece dimensions, results in a total saving of around 10,800 euros for solid material. This means that by using the right saw blade, the cutting performance was increased by 35% and saw blade consumption was reduced by 58%. Isn’t that a pretty clear result?

Conclusion: A myth that costs more than it helps
The myth of the universal band saw blade persists, but practice shows that the optimum choice of band saw blade significantly increases both the cutting performance and the efficiency of a band saw. The targeted use of the right saw blades for band saws not only reduces machine times, but also tool costs considerably. Recognizing the differences between saw blades and consequently choosing the right band saw blade are decisive factors for operating costs in metal processing. Once again, the idea of a universal band saw blade may sound tempting, but the truth is that customized solutions are the key to an efficient and cost-effective production process.
Further questions on the topic?
As the report shows, the subject of band saw blades is a very complicated one. Accordingly, expert advice to guide you through the jungle of these special and different band saw blades is very valuable. We have answered some recurring questions from our customers on the subject in a question-and-answer catalog for better understanding.

Leave A Comment